匯成化工小編帶來磷化液在使用中的一些誤區
作者:admin 發布日期:2019/8/24 14:46:04
匯成化工小編帶來磷化液在使用中的一些誤區
1.磷化液在使用中存在諸多誤區,如長時間在常溫或更低的溫度下使用、高濃度下使用、不顧條件地降低磷化時間、使用地下水或污水配制磷化槽液、不重視前處理工藝流程等。產生這些誤區既有直接原因,又有間接原因。
直接原因:一是有關企業為了降低生產成本,不顧產品質量;二是減少設備投資,導致“湊合使用”;三是輕易相信某些供應商的虛假宣傳。
間接原因:一是企業缺乏相關技術人員和管理人員,想當然地使用磷化液;二是受某些行業初始技術、工藝水平、工藝裝備的影響,認為既有的工藝就是完全正確的;三是通過不正當競爭使用質量低劣的磷化液。
存在如此多的誤區,企業不能很好地使用磷化液,導致磷化液浪費嚴重、磷化膜質量低下、生產成本加大、污染物處理難度加大、污物處理費用升高。
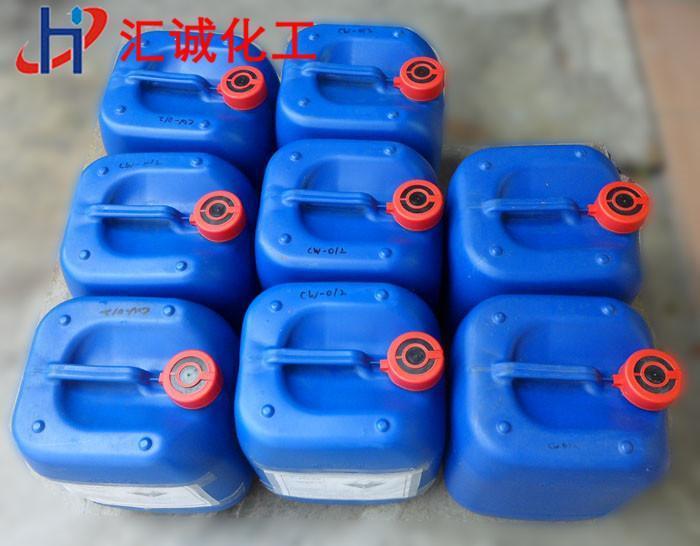
2.1 磷化溫度越低越好
有關磷化溫度,行業中往往存在一些誤區,認為最好在常溫或更低的溫度下長時間使用磷化液。殊不知在溫度一定的情況下,為了滿足生產節拍和質量,往往需要加大藥劑使用濃度或延長處理時間來彌補溫度的不足。
根據磷化反應原理,升高溫度可以加快磷化反應速度,有利于磷化反應的進行。在相當多的中小企業,往往都采用常溫磷化,甚至在冬季也不加溫,磷化液多數情況下都呈黑色。
我們知道,溫度過低時不利于磷酸電離,磷化液中游離的PO43-過低,很難形成磷化膜,而此時磷化液中的游離磷酸又過高,快速腐蝕金屬使大量的Fe2+進入磷化液中,磷化液很快變黑。同時溫度過低,削弱了NO3–和NO2-的氧化性又進一步加快了磷化液變黑的速度。從式(3)可以看出,溫度過低不利于Fe(NO)2+分解。
以亞硝酸鹽為主要促進劑的磷化液,NO與Fe2+在上述溫度下形成穩定的深棕色絡離子Fe(NO)2+,過多時就變成了黑色。反應原理如下:
Fe2++NO2-+2H+=Fe3++NO+H2O (1)
Fe2++NO=[Fe(NO)]2+ (2)
可見,反應后生成的NO并沒有從溶液中溢出,而是與Fe2+結合成亞硝基配合物。式(1)和式(2)在實驗室稱作“棕色環”反應。
注意,式(1)是Fe2+與NO2-反應,而不是Fe2+與NO3–反應,原因是Fe2+與NO3–必須在濃硫酸等強酸性條件下才能發生式(1)的反應,而Fe2+與NO2-在磷酸等弱酸性條件下就可以發生式(1)的反應,這恰好符合磷化液的工作條件。生成的Fe(NO)2+在工作狀態的磷化液中能穩定存在,在磷化液溫度升高時不穩定,發生分解并溢出NO。反應如下:
[Fe(NO)]2+=Fe2++NO↑ (3)
但是溫度超過一定限度,副反應增多,磷化液自身消耗,生成額外沉渣。不管磷化液工作還是不工作,額外生成沉渣都存在。原因如下:溫度升高,加快磷酸二氫根電離生成大量的PO43-離子,在Zn2+離子含量一定時,兩者的濃度滿足Zn3(PO4)2的溶度積時便生成Zn3(PO4)2沉淀,即額外沉渣。反應如下:
H2PO4-=2H++PO43- (4)
3Zn2++2PO43-=Zn3(PO4)2↓ (5)
正常情況下,溫度升高,會有少量的額外沉渣生成。當溫度超高上限時,破壞了正常溫度下的槽液平衡,原有的游離酸度、總酸度和酸比值會打破,需要重新建立新溫度下的槽液平衡,即升高了游離酸度,降低了總酸度和酸比值,也就是說額外消耗總酸度生成大量沉渣。
式(5)對于溫度來說是不可逆的。也就是說,一旦槽液溫度超過上限生成沉渣,再降低溫度不能回復槽液原有的游離酸度、總酸度和酸比值,必須通過加入新鮮磷化液的辦法才能回復槽液原有的參數。磷化液的加熱系統最好采用合格的自動溫度控制系統,并設有溫度上限報警裝置。無自動控制系統時需要人工參與控制,嚴禁溫度超過上限。
目前,多數涂裝企業的磷化溫度都在30-45℃之間。
2.2 磷化液濃度越高越好
實際工作中,磷化液的濃度是通過其酸度來控制的。磷化液的酸度包括總酸度、游離酸度。
總酸度:磷化工作液的總酸度,對磷化膜的完整性有直接影響。當總酸度低于下限時,不能形成完整的磷化膜,而高于上限時,生成的磷化膜粗糙,甚至掛灰。
正常使用時涂裝磷化液的總酸度控制在15-25點之間。
游離酸度:在一定范圍內,游離酸度升高,磷化膜溶解加快,膜重降低,基體的腐蝕迅速增加。游離酸度過高,難以形成磷化膜;游離酸度過低,基體溶解非常慢,磷化膜的生成也慢,甚至導致磷化液不能正常工作。
正常使用時涂裝磷化液的游離酸度控制在0.5-1.2點之間。
如果游離酸度和總酸度都低,則加入磷化濃縮液;如果游離酸度和總酸度都高,則加水稀釋;如果游離酸度低但總酸度高,則先加入磷化液后再進行稀釋;如果游離酸度高但總酸度低,則先加入中和劑調整游離酸度,之后再加入磷化液調整總酸度。
一般情況無論是浸泡式磷化還是噴淋式磷化,建槽時的濃度控制在5%或以下。
2.3 噴淋壓力越高越好
隨著噴淋壓力的升高,磷化反應速度加快,有利于磷化進行。但壓力過大,工件表面來不及發生化學反應,即被機械沖力破壞,也不利于生產線節能。
正常使用時磷化液的噴淋壓力控制在0.05-0.12Mpa之間。
2.4 磷化時間越短越好
如果磷化時間過短,形成的磷化膜不完整或難以形成磷化膜。隨著磷化時間的延長,磷化膜重增加,可使磷化膜細致均勻。但磷化時間過長,耐蝕性反而下降。浸泡工藝的磷化時間比噴淋工藝的時間長。
實踐中需要注意克服兩點:一是一味地縮短磷化時間,二是一味地延長磷化時間。在其它條件一定的情況下,噴淋磷化時間一般為1.5-3.0分鐘,浸泡磷化時間一般為5-20分鐘。有些企業為了滿足生產節拍,不顧自身條件的限制,將浸泡磷化的處理時間限制在3分鐘內,導致磷化膜不完整問題,尤其是酸洗后的厚重工件在如此短暫的時間內難以生成完整的磷化膜,這是不可取的。還有一些企業常溫使用磷化液,遇到工件表面氧化膜較厚時將噴淋磷化時間延長至5分鐘以上或將浸泡磷化時間延長至30分鐘以上,導致磷化膜過厚、粗糙,同樣是不可取的。
必須根據磷化液的組成與性質、磷化溫度、機械外力、磷化液濃度以及工件表面狀態等來選擇合適的磷化時間。
2.5 一味地延長磷化液壽命
磷化液在工作時,各種組分不是按照配比消耗的,需要通過添加液來調整,所以磷化液最好分建槽液和添加液,建槽時使用建槽液,添加時使用添加液。通過不斷補充來維持磷化液穩定,同時還要保證酸比一直在預定的合理的范圍內。正常情況下,質量優良的磷化液通過補充母液,即可保證游離酸度、總酸度以及它們的比值在預定范圍內,不需要通過加入中和劑來降低不斷升高的游離酸度或者通過加入磷酸或硝酸來提高不斷下降的游離酸度。
如果磷化液的總酸度和游離酸度均在正常范圍,但磷化液中的污染物如SO42-、Cl-、Al3+等積累過多或出現大量綠色絮狀懸浮物,磷化反應時間延長,磷化膜不均勻,抗蝕性能下降,沉渣增多,則表明磷化工作液中的組分比例失調,只好重新建槽。應嚴格控制SO42-、Cl-、Al3+進入磷化液中。
2.6 向磷化槽液中額外加入中和劑
如果磷化濃縮液中的總酸度與游離酸度的比例不合適,如酸比值偏小,在不斷添加的情況下導致工作液的游離酸度一直在高位甚至超過高位下運行,需要加入中和劑降低游離酸度,生成的PO43-離子進一步與Zn2+離子結合,產生額外沉渣。如果工件表面含有堿性物質時,也同樣會產生額外沉渣。這樣會白白浪費磷化液,加大了生產線維護及污物處理成本。
之所以出現這樣的情況,其根本原因是用戶圖便宜,使用了質量差的磷化液。正確做法是,更換質量上乘的磷化液。對于不符合企業標準的磷化液,嚴禁采購。
2.7 不同廠家的磷化液混用
由于某種原因,用戶需要更換磷化液,又不想丟棄原有的庫存磷化液,于是將新購進的其它廠家的磷化液與原庫存磷化液混用。由于用戶不清楚這兩個廠家磷化液的組成及配比,又輕易相信廠家的宣傳,導致混合后出現沉渣、磷化速度及質量下降、消耗量增多甚至停止生產等后果。
2.8 磷化液使用中不夠穩定
由于國內磷化液生產廠家眾多,質量參差不齊,使用過程常出現以下不穩定情況。
2.8.1游離酸度不斷升高,總酸度不斷下降
這是質量很差的磷化液,使用時需要不斷加入中和劑來降低游離酸度,說明磷化液的有效組分并沒有完全用于生成磷化膜。總酸度不斷降低,說明磷化液中的有效組成偏低,所以消耗量很大。不僅如此,使用這種磷化液,經常導致磷化膜不完整、發黃生銹、疏松、粗糙等,磷化質量很難滿足要求,根本原因是添加液酸比過低或Zn2+濃度過低,屬于配比不合理。
2.8.2游離酸度不斷下降,總酸度不斷升高
由于游離酸度不斷下降,正常添加磷化液無法滿足游離酸度的要求,需要加入磷酸等組分提高游離酸度。總酸度不斷升高,說明磷化液中的有效組分含量高。這種磷化液使用中產生的沉渣異常多,說明有效組分并沒有完全用于生成磷化膜,而是生成了沉淀,所以消耗也很大。所生成的磷化膜一般比較薄,質量相對來說較穩定。根本原因是添加液的酸比過高或鋅離子含量過高,屬于配比不合理。
2.8.3游離酸度不斷下降,總酸度不斷下降
這樣的磷化液組成與配比是合理的,但是消耗量大,所得磷化膜的質量一般都很穩定,也能滿足質量要求。根本原因是供應商為了降低成本,有意降低有效物質含量。這樣的磷化液一般價格都比較低,但是用量卻很大。如果從磷化液消耗成本來考慮,用戶使用這樣的磷化液不一定經濟合理。由于用量大,需要用戶的操作人員頻繁補加,增加了操作人員的勞動強度,也需要用戶現場保有相當數量的添加液以保證正常添加。
2.8.4游離酸度不斷升高,總酸度不斷升高
這是質量優良的磷化液。正常添加時,酸度升高,說明磷化液中的有效物質含量高,消耗量少。減少磷化液的添加量或加水稀釋工作液,就可以解決此問題。
2.9 只要給磷化液加熱就可以
2.9.1電加熱
為了快速升高磷化槽液的溫度,使用大功率電加熱器對磷化液直接加熱,導致磷化液局部溫度過高,遠遠高于磷化液的溫度上限,加快了磷酸二氫根的電離,最終生成大量沉渣,白白浪費磷化液。
2.9.2熱水或蒸汽直接加熱磷化液
與電加熱器相比,蒸汽直接加熱對磷化液的損害更大。其一是導致磷化液局部溫度過高,生成沉渣;其二是蒸汽冷凝水直接進入到磷化液中,稀釋磷化液,導致工藝參數波動很大,需要頻繁調整磷化液,不僅浪費磷化液,還會使磷化質量難于滿足要求。
2.9.3蒸汽換熱
雖然有換熱器,但是加熱介質使用蒸汽。由于蒸汽溫度高,通過換熱器加熱磷化液時,會使換熱器表面的磷化液溫度很高,遠高于其溫度上限,導致出現大量沉渣。這些沉渣很快堵塞管道,若不及時清理,加熱器便不起作用,嚴重浪費磷化液。
如果采用熱水為加熱介質,如果水溫過高也存在同樣的問題。一般說來,加熱介質與磷化液的溫差控制在10-20℃較為合適。
2.10 使用地下水或污水配制磷化槽液
磷化的工藝用水應滿足航空航天部標準《金屬鍍覆和化學覆蓋工藝用水水質規范》(HB5472-1991)的要求。如果水質過硬即鈣、鎂離子過多,工藝用水在不斷地添加過程中會導致磷化液的游離酸度降低,生成的PO43-離子進一步與Zn2+、Ga2+、Mg2+離子結合,產生額外沉渣,浪費磷化液,污物處理費用增加。原理如下:
2HCO3-+H2PO4-=2CO2↑+PO43-+2H2O (6)
2.11 多種金屬不能在同一槽液中處理
工業生產中,往往需要處理鋼鐵、鋁及鋁合金、鋅及鋅合金的金屬材質。隨著技術進步,目前出現了能夠同時處理鋼鐵、鋁及鋁合金、鋅及鋅合金等不同金屬的磷化液,而且在同一槽中完成,縮短了工藝流程,也減少了磷化液及能源的浪費。
當材料為鋼-鋁組合件時,這種選擇顯得尤為重要。選擇合適的磷化液,在噴淋生產線,可以進行批處理、混裝處理、組合件處理;在浸泡生產線,可以進行批處理、組合件處理。
2.12 長時間不加或一次性大量加入磷化液
一些企業認為,只要磷化液能用,就可以不加磷化原液,直至不能滿足要求時再一次性大量加入,這種做法很不合理。一是磷化液長時間使用,各種組分都在消耗,而且不是按配比的比例消耗的,導致磷化性能急劇下降,甚至報廢,需要一次性加入大量磷化原液來調整。即使這樣,也很難恢復磷化液的最初性能,很難預防磷化缺陷的發生。另一方面,一次性大量加入磷化原液,導致槽液組成及濃度大幅波動,無法滿足磷化質量的恒定,藥劑浪費嚴重。
2.13 長時間不加或一次性大量加入促進劑
促進劑偏低,磷化膜泛黃,需要酸洗后重新磷化。促進劑偏高,一方面將大量的Fe2+離子氧化成Fe3+離子,進而是生成FePO4沉渣,另一方面促進劑揮發時會生成水,使磷化液的pH值升高,導致額外生成Zn3(PO4)沉渣,浪費藥劑,生產成本增加,污物處理費用增加。
2.14 不注重前處理工藝流程
前處理工藝流程不合理引發的質量事故比比皆是,必須引起足夠重視。目前,國內涂裝制造業的前處理工藝流程五花八門,涂裝質量參差不齊,原輔材料浪費嚴重,污染物處理費用增加。
2.14.1典型問題流程一——工藝流程過短,不適合鋅系磷化
原工藝流程:脫脂-水洗-酸洗-鋅系磷化
實際操作是:酸洗后返回前面的水洗,水洗后從上方繞過酸洗槽,進入磷化,磷化后從上方繞過酸洗槽進行水洗,水洗后從上方繞過酸洗槽、磷化槽后下件。可想而知,如此得到的磷化膜根本達不到國家標準GB/T6807-2001的技術指標。工件來回從酸洗、磷化等上方移動,工件工序間閃銹,滴液相互污染槽液,最終導致槽液浪費嚴重,甚至報廢。
該工藝流程優化如下:酸洗除油-水洗-鐵系磷化-水洗
2.14.2典型問題流程二——工位順序不合理
原工藝流程:酸洗-水洗1-水洗2-脫脂-水洗3-水洗4-表調-鋅系磷化-水洗5-水洗6
實際操作是:第一步驟為脫脂,脫脂后進入水洗3、水洗4,從水洗4、水洗3、脫脂、水洗2、水洗1上方繞過進入酸洗,酸洗后進入水洗1、水洗2,從脫脂、水洗3、水洗4上方繞過進入表調,之后按順序進行。涂裝企業認為,將酸洗工位設置在邊緣,不會污染槽液,同時有利于酸氣的排出。事實上,水洗2后,工件較長時間在藥劑槽的上方移動,會導致工序間閃銹,不但磷化質量不合格,還會過多地消耗磷化,浪費原材料。
該工藝流程優化如下:脫脂-水洗1-水洗2-酸洗-水洗3-水洗4-表調-鋅系磷化-水洗5-水洗6
2.14.3典型問題流程三——多種金屬分線處理
原工藝流程:預脫脂-脫脂-水洗1-水洗2-酸洗-水洗3-水洗4-表調-鋅系磷化-水洗5-水洗6-硅烷處理-水洗7-純水洗8-鈍化-水洗9-純水洗10
實際操作是:對于鋼鐵工件,實施“預脫脂-脫脂-水洗1-水洗2-表調-鋅系磷化-水洗5-水洗6”,中間越過“-酸洗-水洗3-水洗4”和“-硅烷處理-水洗7-純水洗8-鈍化-水洗9-純水洗10”;對于鋅及鋅合金件,實施“預脫脂-脫脂-水洗1-水洗2”和“-硅烷處理-水洗7-純水洗8”,中間越過“-酸洗-水洗3-水洗4-表調-鋅系磷化-水洗5-水洗6”和“-鈍化-水洗9-純水洗10”;對于鋁及鋁合金件,實施“預脫脂-脫脂-水洗1-水洗2-酸洗-水洗3-水洗4”和“-鈍化-水洗9-純水洗10”,中間越過“-表調-鋅系磷化-水洗5-水洗6-硅烷處理-水洗7-純水洗8”。從流程上看,水洗工位過多,不利于節約用水。其次,由于工藝流程過長,導致投資增加,占地增加。另外,導致槽液間相互污染。
該工藝流程優化如下:預脫脂-脫脂-水洗1-水洗2-表調-鋅系磷化-水洗5-(純)水洗6
2.14.4典型問題流程四——酸洗后無中和
對于結構簡單的銹蝕冷軋板,酸洗后無中和是可以的。但是對于結構復雜、焊點多、夾縫多或厚重熱軋板應當設置中和工位。一方面后者容易將殘留的酸帶入表調并很快使表調失效,進而導致磷化液游離酸度升高,需要頻繁調整磷化液工作參數,另一方面后者也會將工件上過多的亞鐵離子帶入表調并使表調很快失效,進而導致磷化液中的亞鐵離子過高,產生過多沉渣。
原工藝流程:脫脂-水洗1-水洗2-酸洗-水洗3-水洗4-表調-鋅系磷化-水洗5-水洗6
該工藝流程優化如下:脫脂-水洗1-水洗2-酸洗-水洗3-水洗4-中和-水洗5-水洗6-表調-鋅系磷化-水洗7-水洗8
2.14.5典型問題流程五——酸洗或中和后無水洗
原工藝流程1:脫脂-水洗1-水洗2-酸洗-表調-鋅系磷化-水洗3-水洗4
原工藝流程2:脫脂-水洗1-水洗2-酸洗-水洗3-水洗4-中和-表調-鋅系磷化-水洗5-水洗6
酸洗或中和后無水洗,都會將工件表面攜帶的酸或堿帶入表調,引起表調失效,進而導致磷化液的游離酸度頻繁升高或降低,嚴重影響磷化膜的質量,還會浪費藥劑。當酸根為Cl-或S042-時,會嚴重降低磷化膜的耐腐蝕性。
優化后的工藝流程:
工藝流程1:脫脂-水洗1-水洗2-酸洗-水洗3-水洗4-表調-鋅系磷化-水洗5-水洗6
工藝流程2:脫脂-水洗1-水洗2-酸洗-水洗3-水洗4-中和-水洗5-水洗6-表調-鋅系磷化-水洗7-水洗8
2.14.6典型問題流程六——酸洗與中和之間無水洗
原工藝流程:脫脂-水洗1-酸洗-中和-水洗2-表調-鋅系磷化-水洗3
原則上講,這樣的流程不適合處理結構復雜、焊點多、夾縫多或厚重熱軋板。對于結構簡單的銹蝕冷軋板,將中和改為水洗即可。酸洗后,工件表面攜帶有大量的酸和亞鐵離子,進入中和后,亞鐵離子迅速轉化為氫氧化亞鐵附著在工件表面,在空氣的作用下,外層很快轉化為氫氧化鐵,有時也稱“工序間閃銹”。發生閃銹的工件磷化時,會大量消耗磷化液的游離酸度,沉渣量大,極大地浪費磷化液,同時嚴重惡化磷化膜質量。這種情況下,表調很快失效,產生極大浪費。解決問題的關鍵,就是增加一個水洗槽。
該工藝流程優化如下:脫脂-水洗1-酸洗-水洗2-中和-水洗3-表調-鋅系磷化-水洗4
2.15 不考慮生產負荷
現代自動生產磷化線,一般在設計時就已經考慮了單位時間內處理的工件面積與磷化槽液體積之間的關系,所以很少出現因負荷偏大引起大量沉渣現象。但是在老的生產線或半自動、手工操作的生產線上,由于當時對磷化質量要求不是很高或工藝、管理等不完善,時常有大量的沉渣生成。
在這種情況下,單位時間內處理的工件面積過大,磷化液又過少,導致在磷化過程中磷化液的游離酸度和總酸度大幅波動,且游離酸度波動的幅度遠大于總酸度波動的幅度,生成大量沉渣。工件表面生成結晶粗大的磷化膜,遠離表面區域自行生成沉渣白白耗費藥液。為了恢復槽液原有的功能,需要頻繁添加磷化液,導致惡性循環,難于保證磷化膜質量,藥劑浪費十分嚴重。
2.16 浸泡就是工件及槽液都靜止不動
所謂浸泡,就是將需要處理的金屬材料浸漬在磷化槽中完成磷化的過程。顯然,浸泡包括動浸泡和靜浸泡兩種方式。動浸泡是使槽內液體循環或令工件抖動,靜浸泡是指槽內液體和工件都不動。靜浸泡沒有機械沖刷的輔助作用,因此磷化速度相對較慢,處理時間較長。動浸泡方式的處理效果更好些,有利于工件及時接觸到新鮮磷化液,縮短磷化時間,提高磷化質量。
有些企業疏于對槽液的管理,不能及時清理磷化槽內的沉渣。在槽液循環時,大量沉渣泛起附著于磷化膜表面,導致磷化膜掛灰,所以認為槽液循環對磷化不利,這是對槽液循環的誤解。
3 結論
磷化液在使用中存在諸多誤區,如長時間在常溫或更低的溫度下使用、高濃度下使用、不顧條件低降低磷化時間、使用地下水或污水配制磷化槽液、不注重前處理工藝流程等。產生這些誤區既有直接原因,又有間接原因。這些誤區的存在,導致企業不能很好地使用磷化液,磷化液浪費嚴重、磷化膜質量低下、生產成本加大、污染物處理難度加大、污物處理費用升高。
此文關鍵字:
西安磷化液廠家|西安磷化液價格